Case Studies: Businesses That Successfully Reduced Costs While Enhancing Quality
In today’s competitive market, businesses face the dual challenge of reducing operational costs while maintaining high-quality standards. It’s a balancing act that can seem impossible at times, but many companies have successfully navigated this path. This article highlights case studies of businesses that have implemented innovative strategies to cut costs without compromising on quality, providing you with insights and inspiration for your own organizational challenges.
Case Study 1: Toyota’s Lean Manufacturing
Toyota has long been recognized for its lean manufacturing principles, which focus on eliminating waste in all forms. By streamlining production processes and encouraging continuous improvement through employee input (known as ‘Kaizen’), Toyota reduced operational costs significantly while enhancing the quality of its vehicles. The company’s commitment to just-in-time production ensures that resources are used efficiently, leading to lower inventory costs and higher product quality.
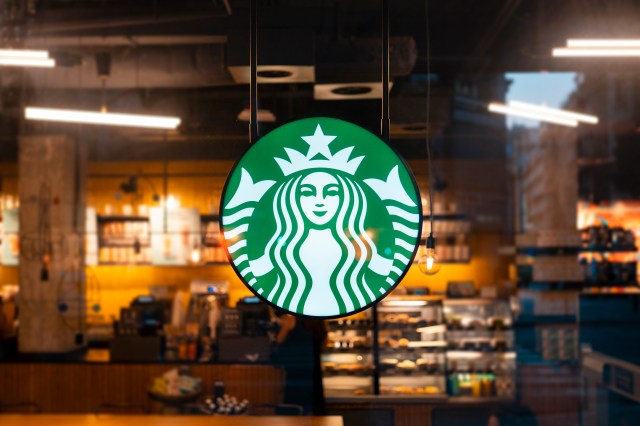
Case Study 2: Starbucks’ Use of Technology
Starbucks is an excellent example of how technology can aid in reducing operational costs while improving customer experience. By implementing mobile ordering and payment systems, Starbucks has streamlined its operations and reduced wait times for customers. This not only cuts labor costs associated with in-store service but also enhances the overall quality of customer interaction by providing a more efficient service.
Case Study 3: Amazon’s Supply Chain Optimization
Amazon has revolutionized e-commerce logistics through strategic supply chain optimization. By utilizing advanced data analytics and automation technologies in their warehouses, Amazon has been able to reduce shipping times and associated costs dramatically. The company’s focus on optimizing delivery routes and inventory management ensures that customers receive high-quality service without delays or errors.
Case Study 4: Procter & Gamble’s Innovation Strategy
Procter & Gamble (P&G) adopted an innovation-driven approach to reduce operational expenses while increasing product quality. By investing in research and development, P&G was able to create innovative products that require fewer raw materials to produce without sacrificing efficacy or consumer satisfaction. Their commitment to sustainability further enhances their brand reputation while cutting down on material costs.
Case Study 5: Dell’s Direct Model
Dell transformed the computer manufacturing industry with its direct sales model, allowing customers to build custom computers online before they are manufactured. This model reduces excess inventory costs since products are made based on actual orders rather than forecasts—which often lead to overproduction—while maintaining high-quality standards through direct customer feedback during the purchasing process.
These case studies illustrate that it is indeed possible for businesses to reduce operational costs without sacrificing quality by embracing innovation, technology, lean methodologies, and effective supply chain management practices. Implementing similar strategies tailored to your organization can help you achieve sustainable success in today’s fast-paced business environment.
This text was generated using a large language model, and select text has been reviewed and moderated for purposes such as readability.